6 Different Types of Drywall and Which To Choose
If you’re expanding your building or repairing an older one, make sure to use high-quality materials that match the existing structure and environment. Installing an incompatible material could lead to frequent repairs, compromised energy efficiency, or safety risks over time.
With numerous drywall types available, each designed for specific applications and environments, picking the right material will allow your project to meet building codes and your performance expectations. Learn the different types of drywall and which to choose for your commercial or residential property.
1. Standard Drywall for Interior Construction
Standard drywall, also known as regular gypsum board, is a common option for interior walls and ceilings. This basic drywall type consists of a gypsum core sandwiched between two layers of paper facing. Manufacturers produce standard drywall in various thicknesses, with 1/2-inch and 5/8-inch being the most popular choices for residential and commercial applications.
The 1/2-inch thickness works well for most residential interior walls to provide adequate strength and sound dampening for typical household needs. The 5/8-inch option offers a durable hold and better fire resistance. This makes it suitable for commercial applications or areas requiring additional structural support.
You can easily customize standard drywall with paint, wallpaper, or textured finishes to match any aesthetic. This adaptability makes it a popular choice for both residential and commercial interior spaces.
Standard drywall performs best in dry environments with normal temperature conditions. Contractors often choose this option for bedrooms, living rooms, hallways, and other interior spaces that don't experience high moisture or extreme temperature fluctuations. Standard drywall typically offers the lowest material cost per square foot but will require more maintenance and repairs to boost longevity and performance.
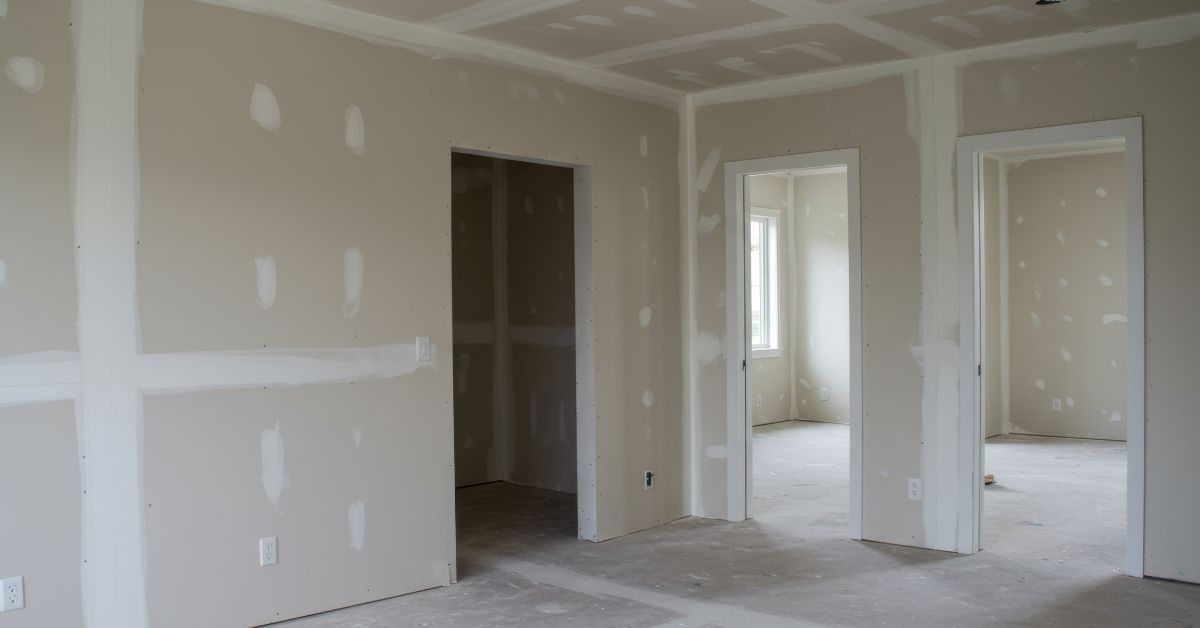
2. Moisture-Resistant Drywall for Protection Against Water Damage
Moisture-resistant drywall, commonly called green board due to its distinctive green paper facing, addresses the challenges of high-humidity environments. This specialized drywall type features a water-resistant core and facing materials that prevent moisture penetration better than standard drywall.
The green board construction includes a moisture-resistant gypsum core and specially treated paper facings that help prevent mold and mildew growth. This protection makes moisture-resistant drywall ideal for bathrooms, laundry rooms, basements, and kitchens with excessive humidity levels.
However, moisture-resistant drywall has limitations, and direct water contact can still cause damage. By performing routine maintenance, you can further extend its lifespan and effectiveness. Regularly inspecting for signs of leaks or water damage and addressing them promptly will help preserve its protective qualities.
Proper installation with appropriate vapor barriers and ventilation systems will lessen the risks of damage. Many contractors recommend using moisture-resistant drywall as part of a comprehensive moisture management strategy rather than relying on it as the sole protection method.
3. Mold-Resistant Drywall for Challenging Environments
Mold-resistant drywall incorporates mold-inhibiting materials throughout the entire board construction. Unlike moisture-resistant drywall that relies primarily on treated paper facings, mold-resistant drywall features a specially formulated gypsum core designed to resist mold growth even under challenging conditions.
This advanced drywall type excels in environments prone to condensation, high humidity, or occasional moisture exposure. Contractors frequently specify mold-resistant drywall for basement finishing, bathroom installations, and commercial applications susceptible to mold for health and liability reasons. Its ability to prevent mold growth helps create safer, healthier environments for both employees and visitors in health care facilities particularly.
The boosted protection comes with slightly higher material costs, but the long-term benefits often justify the investment. Reduced maintenance, fewer health concerns, and improved indoor air quality make mold-resistant drywall an attractive option for quality-focused projects.
4. Fire-Resistant Drywall To Enhance Safety
Fire-resistant drywall, also known as Type X drywall, incorporates special additives in the gypsum core that slow the spread of flames and provide additional fire protection. Building codes often require fire-resistant drywall in specific applications, including walls separating living spaces from garages, furnace rooms, and certain commercial occupancies.
Glass fiber reinforcements and other additives help the drywall maintain structural integrity longer during fire exposure. Type X drywall typically provides 60 minutes of fire resistance when properly installed according to manufacturer specifications and building code requirements.
Fire-resistant drywall serves dual purposes by providing both standard wall finishing capabilities and fire protection, making it an expensive option for project managers compared to other drywall types. The additional upfront investment frequently pays dividends through improved durability and functionality.
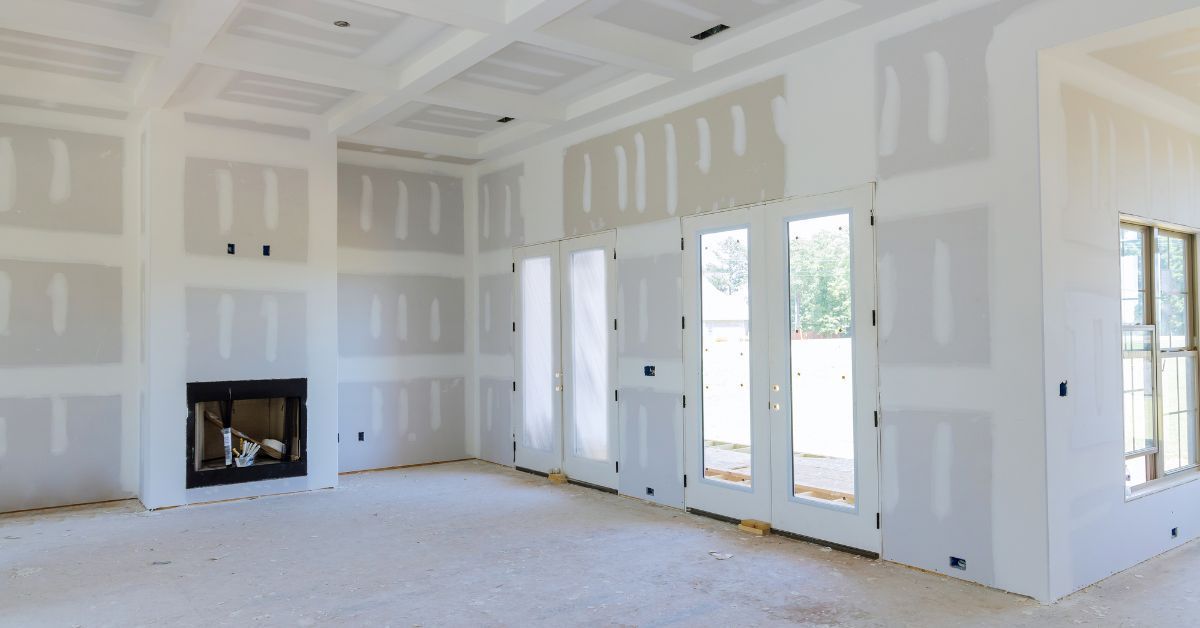
5. Soundproof Drywall for Controlling Noise Transmission
Soundproof drywall addresses noise control challenges that come from densely populated properties. This drywall type features a higher-density gypsum core and sometimes includes sound-dampening materials that reduce sound transmission between rooms or floors.
Acoustic drywall works particularly well in home theaters, recording studios, and multifamily housing. The sound-dampening properties create more comfortable living and working environments by reducing unwanted noise transmission. For commercial buildings, this allows for uninterrupted workflow.
Proper sealing and attachment methods impact the acoustic performance of the installation. Contractors often combine soundproof drywall with other noise-control strategies for optimal results. This includes using acoustic sealants, insulation, or resilient channels during installation.
6. Paperless Drywall for Durability Without Paper Facing
Paperless drywall eliminates traditional paper facings in favor of fiberglass mat facings that provide superior moisture and mold resistance. This innovative construction approach addresses many of the weaknesses associated with paper-faced drywall while maintaining excellent workability and finishing characteristics.
The fiberglass facing material resists tearing, moisture penetration, and mold growth better than traditional paper facings. This makes paperless drywall suitable for challenging applications such as basements and bathrooms.
Its durability also makes it an excellent choice for schools, hospitals, and commercial buildings, where walls are more prone to wear and tear. The fiberglass facing resists damage and reduces the need for frequent repairs.
Paperless drywall typically costs more than standard options, but the proven durability and reduced maintenance requirements often provide excellent long-term value. Contractors appreciate the improved workability and reduced callback potential that paperless drywall offers.
Whether you’re prioritizing moisture resistance, fire safety, or soundproofing, learning about the different types of drywall and which to choose will allow you to enhance both the functionality and longevity of your space. At Rival Drywall, our specialists will help you find compatible equipment that matches your project requirements and budget. Partner with our commercial drywall contractors in Denver, CO to get high-quality materials and service for your next project today.